Thermochemical & heat treatment
Development and industrialization of thermochemical and heat treatment processes
Performance requirements for mechanical parts are becoming increasingly stringent: fatigue resistance, corrosion resistance, tribological behavior, complex geometries, noise reduction, etc.
IRT M2P develops and optimizes processes that meet and go further than current specifications while also striving to be more cost competitive and environmentally friendly. Through our semi-industrial scale equipment, we reproduce industrial conditions in order to obtain reliable metallurgical data to model and then optimize thermochemical and heat treatment processes.
Expertise & Services
R&D studies and services in thermochemical and heat treatment
- Implementation of thermochemical treatment, vacuum heating, cryogenic and gas quenching
- Development and optimization of treatment ranges
- Development of specific recipes (carburizing, nitriding, etc.)
- Study of the influence of thermochemical treatment on the performance of materials (fatigue resistance, tribological behavior)
- Hybridization of technologies
- Development carried out on prototype parts including technical and economic feasibility studies
- Water spray quenching of long products (rods, tubes, and plates)
- Quenching via surface induction heating
- Consumption monitoring, production costs estimation
- Study of the environmental impact of various thermochemical and heat treatment processes
Characterization, material control and chemical analysis
- Metallography (optical microscope, SEM, micro-hardness)
- Chemical analysis (GDOES, ICP, XRD, OES, etc.)
Simulation
- Phase diagrams, diffusion (Thermo-Calc, DICTRA)
- Modeling of solid/gas interactions and phase transformations related to composition gradients (Carbon, Nitrogen)
- Prediction of residual stress profiles
- Determination of heat transfer coefficients by numerical calculation
- Optimization of treatment by numerical simulation
Technology
IRT M2P is equipped with state-of-the-art industrial pilots, for the development, optimization, and modeling of thermochemical and heat treatments. All available equipment is scalable and equipped with various sensors and process logic controls allowing real-time data acquisition and analysis and advanced tools for optimizing processes.
Low pressure carburizing and carbonitriding, gas quenching up to 20 bars
Material properties are optimized by the control of process parameters during enrichment step (treatment time, temperature, chamber pressure, injected gas flow) and during quenching (duration, pressure, turbine speed)
Clean parts, low gas consumption and reduction of deformations, treatment of complex geometries
Gas nitriding at atmospheric/low pressure, oxynitriding, nitrocarburizing
Homogeneity of the treatment atmosphere, precise control of process parameters (temperature, pressure, holding time, carbon and nitrogen enrichments: gas flow rates, KN, KC), pre- and post-oxidation treatments)
Ion nitriding
Control of iron nitrides layers for tribological applications
Nitriding of stainless steels
Improve health and safety conditions
Nitriding in austenitic phase
Keeping stainless properties of steels after nitriding
Reduction of the time of treatment and increase of treated layers depths
Contour hardening by induction quenching
Control of the quenching depth to optimize materials properties gradients
Possible automation
Productivity gains compared to traditional thermochemical treatments
Cryogenic quenching
Control of phase proportions
Spray quenching (water, air, biphasic) of long products
Control and experimental simulation of quenching conditions used in industry
Calculation of heat transfer coefficient using the inverse method
Equipment @M2P
Low pressure carbonitriding furnace
T°max: 1050 °C
Adjustable treatment pressure
Gas quenching: 1 to 20 bars (N2 and/or CO2 and/or He)
Useful area: 650 x 400 x 400 mm GAS
Nitriding furnace
T°working: 200 - 700°C
Atmospheric or low pressure
Useful area: 900 x 600 x 600 mm
Ion nitriding furnace
T°max: 600°C
Plasma technologies: DCPN (Direct Current Plasma Nitriding) or ASPN (Active Screen Plasma Nitriding), Additional heating
Useful area: 800 x 800 mm
Contour hardening platform with induction heating
Simultaneous double frequency generator: 450 kW MF - 200 kW HF
Spray hardening pilot
Instrumentation by 16 thermocouples
Adjustable spray systems (geometries, fluids, pressure, speed)
Cryogenic enclosure
T°working: -100 - 250°C
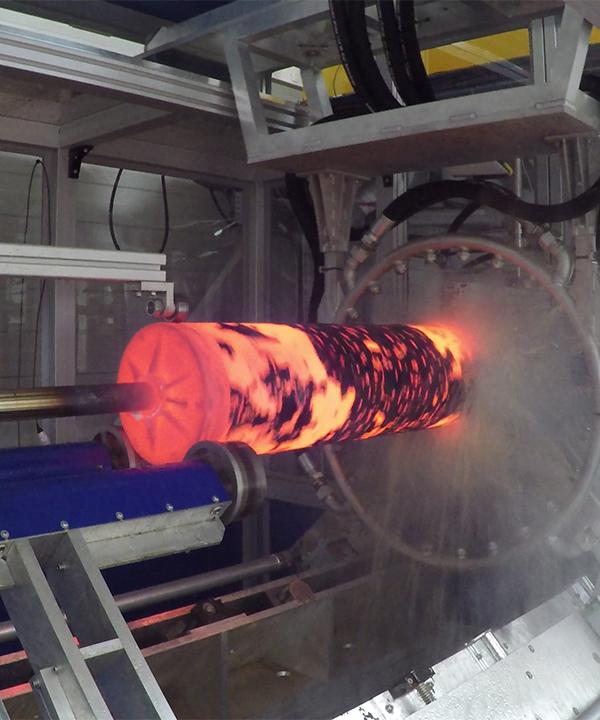
Applications
Surface reinforcement of mechanical parts (gears, bearings, tools, etc.) for the aerospace, automotive, marine, and mechanical fields:
- Increase of fatigue life
- Improvement of tribological properties
Cleaner and more energy efficient processes
Productivity gains by reducing nitriding treatment times, while maintaining mechanical properties
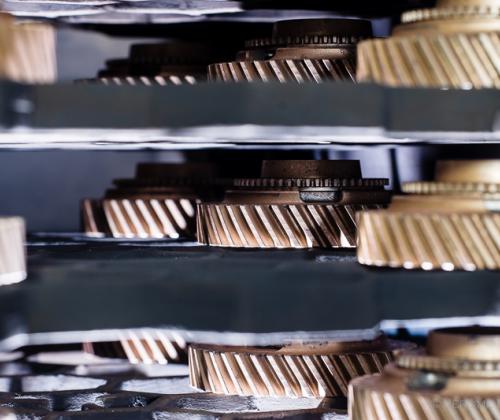