Multimaterials joining
Development and industrialization of joining processes and components for multi-material assemblies

Societal and environmental issues are driving the use of more efficient materials of different types that need to be assembled, hence the need to develop special assembly processes (mechanical or hybrid with welding/ bonding).
IRT M2P aims to innovate in the field of joining processes, developing new hybrid systems to push back the industrial limits of new materials use.
Assemblies mechanical behavior study and the development of dimensioning models allow to predict the feasibility of joints, their service life and to define the optimum process window.
Expertise & Services
- Innovative processes development and associated joining components
- Feasibility of multi-material configurations and process windows definition
- Process monitoring, data acquisition and analysis
- Multi-physics processes simulation: use and development of models, definition of material behaviour constitutive laws
- Characterization of assemblies mechanical behavior
- Single-point and structure scale behaviour modelization
- Development of equivalent models applicable in design offices
- Hybrid processes (bonding and welding)
- Development and understanding of new assembly processes through investment in specific platforms (joining or characterization equipment)
Technology
High speed nailing
- Without pre-hole
- Joining time: 1s
- Only one side access
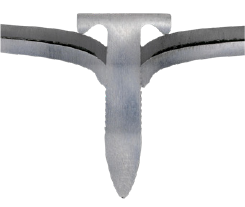
Flow drill screwing
- Possible without pre-hole
- Joining time: 1,5 - 3s
- Only one side access
- Removable component (repairable and recyclable)
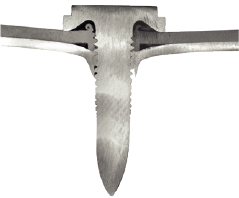
Clinching
- Stamping connection between a punch and a die
- Joining time: 1s
- Two sides access
- No additional component (lightweighting)
- Watertight (sheet integrity)
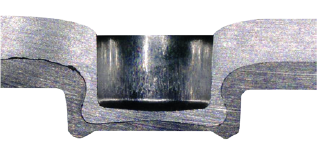
Self-piercing riveting
- Rivet penetration by punching of the top sheet
- Joining time: 1s
- Watertight (bottom sheet integrity)
- Two sides access
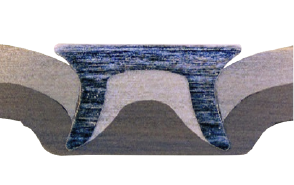
Self-piercing riveting (solid)
- Solid rivet penetration by punching of the top sheet
- Joining time: 1s
- Two sides access
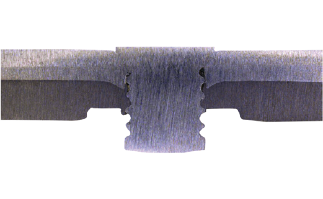
Materials functionalization
- Resistance welded multi-material assembly enabled by the use of inserts
- Local treatments to fit material characteristics to assembly processes
Fasteners
Available toolbox for prototyping some materials, mass treatment and surface treatment of components
Robotization
Industrial representative conditions and processes modeling by taking into account the mistakes brought by the high cadency and the low stiffness of the robotic arms
Working at different levels of maturity (single-point on specimen, multi-point, mini-structures, etc.)
Analysis & Characterization
In support of developments: metallography, quasi-static tests, fatigue, crack propagation monitoring by infrared thermography
Equipment @M2P
Two platforms: Fixed frame / 6 axis robot and associated tools
Nailing system
- Automated pneumatic setting tool with feeding station and process monitoring
Screwing system
- Max. spindle rate 8000 rpm at 15 Nm
- Max. vertical force of 3,6 kN
Clinching tong
- Electrical cylinder 80 kN
- C-frame size 200 mm
Riveting tong
- Self piercing rivets
- Solid punch rivets
- Pneumohydraulic cylinder 80 kN
- C-frame size 250 mm
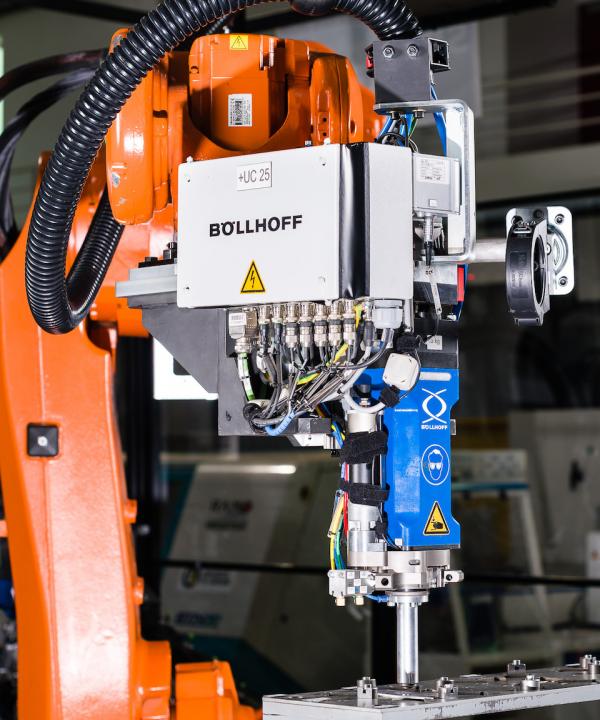
Characterization
- Quasi static testing machine 100 kN
- Fatigue testing machine 100 kN
- Numerical Miscroscopic analysis
- Hardness testing
- NOXCAM640 calibrated infrared camera
Applications
- Lightweight assemblies for automotive body-in-white
- Aluminum on high strength steel
- Hybrid mechanical + welding process development
- Local softening of high strength steel before assembly
- Development of an innovative screw
- Investigations for the aeronautic and other industries