Surface treatment & coatings
Coatings, reinforcement, functionalization and surface finishing on metallic alloys, ceramics and polymers
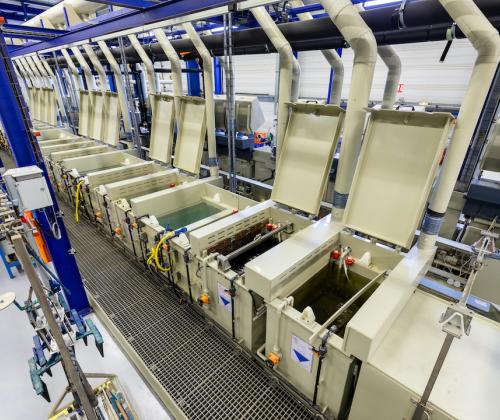
To develop new surface treatment processes, from the laboratory to the industrial scale, to improve performances of materials and coatings, in respect of REACH regulations and SHE constraints (substitution of hexavalent chromium, cyanides, etc.).
IRT M2P contributes to increase the maturity of processes as well as reliability thanks to modular and robotic industrial platforms. These latter enable the development of various types of treatments, metallic coatings and sol gel as well as various post additive manufacturing finishing processes. A platform dedicated to innovative painting applications completes this equipment.
Expertise & Services
Metallic materials and surface treatment processes
Deep knowledge of preparation and surface treatment processes
Deep knowledge of electrolytes (additives, (in)organic complexing agents)
Management of electric parameters (pulsed current)
Formulation of new solutions in surface treatment
Development of coatings by co-deposition
R&D studies and surface treatment services (Al, Mg, Ti alloys, steel and stainless steel)
Development of processes in compliance with environmental regulations
Development of tailor-made surface treatment processes
Development of post-additive manufacturing finishing processes
Robotic application of organic and hybrid coatings
Surface treatment parameters tuning
Maintenance of chemical baths deposition
Recycling of used baths and waste valorisation
Scale transfer support
Processes/ validation at industrial scale
Increase of process maturity and reliability
Set up and transfer of reliable and industrializable analytical methods
Practical and theoretical training
Characterization and control of materials and coatings
Microstructural observations: phase identification, coating morphology (thickness, porosities, etc)
Elementary composition analysis
Surface topography analysis (roughness)
Functional properties evaluation: fatigue resistance, corrosion behaviour, wear resistance, micro-hardness, electrical conductivity, adherence
Simulation (Comsol multi-physics®)
Modelling of metallic structure corrosion behaviour
Modelling of surface treatment processes (equipments sizing, current lines distribution, etc.)
- Study & development of electrolytes, optimisation of pollution control processes
- R&D studies in surface treatment
- Expertise in metallic materials and processes for failure analysis and material characterization
- Study, design and industrialisation of surface treatment equipment
- Supply of all types of test samples (metallic materials)
Technology
Surface preparation and activation
Mechanical (sand-blasting, shot-peening, laser peening); Chemical and Electrochemical ; Solvent degreasing
Light alloys treatments (Al, Ti, Mg)
Chemical conversion (Cr III/Zr, Ti, Cr-free) ; Sulfuric, phosphoric, sulfo-phosphoric, sulfo-tartaric, sulfo-boric anodizations ; Anodized layers (Cr III/Zr, Ni acetate, PTFE) impregnation and sealing ; Hard anodization ; Micro Arcs Oxidation (MAO)
Steels treatments
Chemical plating: copper, nickel (low, middle and high phosphorous) ; Electrochemical plating: nickel (sulfamate, Watt and Wood), trivalent hard chromium, ZnFe high Fe content, ZnNi 12-15%, cyanides-free silver, Zn and alloyed Zn passivations and top-coat ; stainless steels passivations, phosphating (Zn and Mn)
Surface finishing (additive manufacturing & conventional metallurgy)
Chemical polishing ; Electrochemical polishing ; Plasma electrochemical polishing ; Dry Lyte Electropolishing ; Levelling coatings (metallic and sol-gel coatings) ; Tribofinishing
Special processes
Painting application (solvent, water-soluble, powders); Sol-gel coatings ; Aluminium-based metallic ceramic coatings ; Metallicbased hybrid coatings and organic binders ; Zinc flex coatings ; Electrophoresis
Equipment @M2P
SURFACE PREPARATION
Solvent degreasing machines ; Sand-blasting and shot-peening machines
MULTI-SCALE TREATMENTS
Chemical/metallurgical laboratories
3 flexible and instrumented surface treatment lines :
- Pilot line (9 tanks 60L)
- Semi-industrial line (21 tanks 150-300L)
- Semi-industrial line (15 tanks 600L) for the treatment of parts up to 500 kg, including 4 spraying tanks with a volume of 130L
Automated treatment (robot) by immersion and spraying for complex geometries (sol-gel, finishing)
Reverse pulsed current generators (50A to 1500A) • Robotic platform for the treatment by spraying/painting of parts until 1,5 m in length
Dip-spin chamber for bulk processing
Dry Lyte Electropolishing equipment (15L)
Effluent treatment pilot
CHARACTERIZATION
Ionic polisher - Optical microscope ; MEB-FEG ; XRD
3D interference microscope, mechanical profilometer
EDX, ICP-OES, SDL, OHN/CS analyser, X-ray fluorescence
ENOVASENSE®, Deltascope
Macro/micro-hardness instruments
Conductimeter according to MIL DTL 81706
Salt spray (400 and 1000L) according to ISO 9227 - Potensiostats
Taber abraser
Fatigue tests: rotating bending benches, tensile compression cyclic machine
Applications
- REACH compliance: hexavalent chromium substitution
- SHE compliance: cyanides removal on silver processes, ZnFe high Fe content
- Performance optimization: tribological properties, corrosion, temperature, fatigue and wear resistance
- Coatings dedicated to H2 production systems
- Virucide/bactericide coatings
- Surface treatment automatization & processes robotization: painting spray, sol-gel immersion/spraying
- Post-additive manufacturing finishing
- Effluents treatment and valorization
Principal markets:
Aerospace, naval, automotive, building, energy, military, materials/ equipment manufacturers, suppliers of surface treatment, railway, sports/leisure, medical, luxury