Simulation numérique des procédés métallurgiques à l'IRT M2P : un levier technologique pour l'innovation
L’IRT M2P joue un rôle de premier plan dans la recherche et le développement des procédés métallurgiques, couvrant un large spectre d’activités, allant de l’atomisation et la fonderie avancée à l’assemblage multi-matériaux et aux traitements thermiques et thermochimiques. Dans ces domaines, la simulation numérique est devenue un outil incontournable permettant d’optimiser les procédés, de réduire les coûts de développement et d’améliorer la qualité des matériaux et des produites. Cet article explore les apports de la modélisation numérique dans ces trois activités et son impact sur l’industrie.
Simulation et modélisation numérique pour l’atomisation et la fonderie avancée
L’atomisation et la fonderie sont deux procédés fondamentaux pour l’élaboration des matériaux métalliques, utilisés dans des secteurs de pointe tels que l’aéronautique, l’énergie, l’automobile et la fabrication additive. La métallurgie des poudres permet aujourd’hui de repousser les limites traditionnelles de la mise en forme des métaux en offrant des géométries complexes, des propriétés inédites et une optimisation des coûts. Ces avancées dépendent directement de la qualité des poudres métalliques, qui repose sur un contrôle précis des procédés d’atomisation. Parallèlement, la maîtrise des procédés de fonderie est essentielle pour garantir la qualité des semi-produits et la mise en forme de nouveaux alliages à haute performance.
L’IRT M2P s’engage dans cette voie en combinant des équipements de pointe (tours d’atomisation EIGA & VIGA, fours de fonderie PAMCHR & VIM) avec des approches innovantes en simulation numérique pour améliorer la qualité des matériaux produites, ainsi que la performance et l’efficacité industrielle de ces procédés.
La modélisation numérique permet aujourd’hui de mieux comprendre et optimiser ces procédés en simulant les interactions complexes entre les flux de gaz et de métal, les échanges thermiques et la formation des poudres.
Apports de la simulation numérique
La modélisation numérique de ces procédés nous permet de prédire avec précision le comportement du gaz et des métaux lors de l’atomisation et de la fonderie. Nous pouvons analyser la dynamique des fluides, l’interaction gaz/métal, l'échange thermique et la solidification en temps réel. Ces simulations offrent une visualisation des phénomènes invisibles à l’œil nu et aident à affiner les paramètres opératoires.
Ces simulations numériques permettent de :
- Aider l'équipe technique à déterminer le lien entre les paramètres opératoires de la fusion et du gaz.
- Expliquer et trouver des solutions aux problèmes liés à l'écoulement du gaz, tels que le colmatage de la buse, ou à l'écoulement métallique, tels que la solidification proche des parois et loin de la torche.
- Déterminer l’impact de la nature du gaz sur les procédés d’atomisation et de fonderie.
- Fournir une distribution approximative de la taille des particules en fonction des paramètres de fonctionnement pour les procédés d'atomisation.
- Prédire la taille médiane des particules (d50%) en fonction des paramètres opératoires ou de la nuance de l'alliage pour les procédés d'atomisation.
- Fournir la distribution de la température dans le creuset en fonction des caractéristiques du four.
- Identifier les zones de surchauffe ou de refroidissement qui pourraient affecter la qualité du matériau fondu.
- Modéliser les mouvements torche et les trajectoires des inclusions à haute et faible densité.
- Prédire l'épaisseur du bain liquide, la vitesse et le temps de dissolution des inclusions.
- Prédire le comportement des nouveaux alliages dans les différents procédés.
- Optimiser les procédés d'atomisation et de fonderie en déterminant les paramètres opératoires idéaux.
Grâce à ces modèles numériques avancés, il devient possible de mieux comprendre les interactions complexes qui régissent ces procédés et ainsi d’ajuster les paramètres en amont pour garantir une qualité optimale dès la première production.
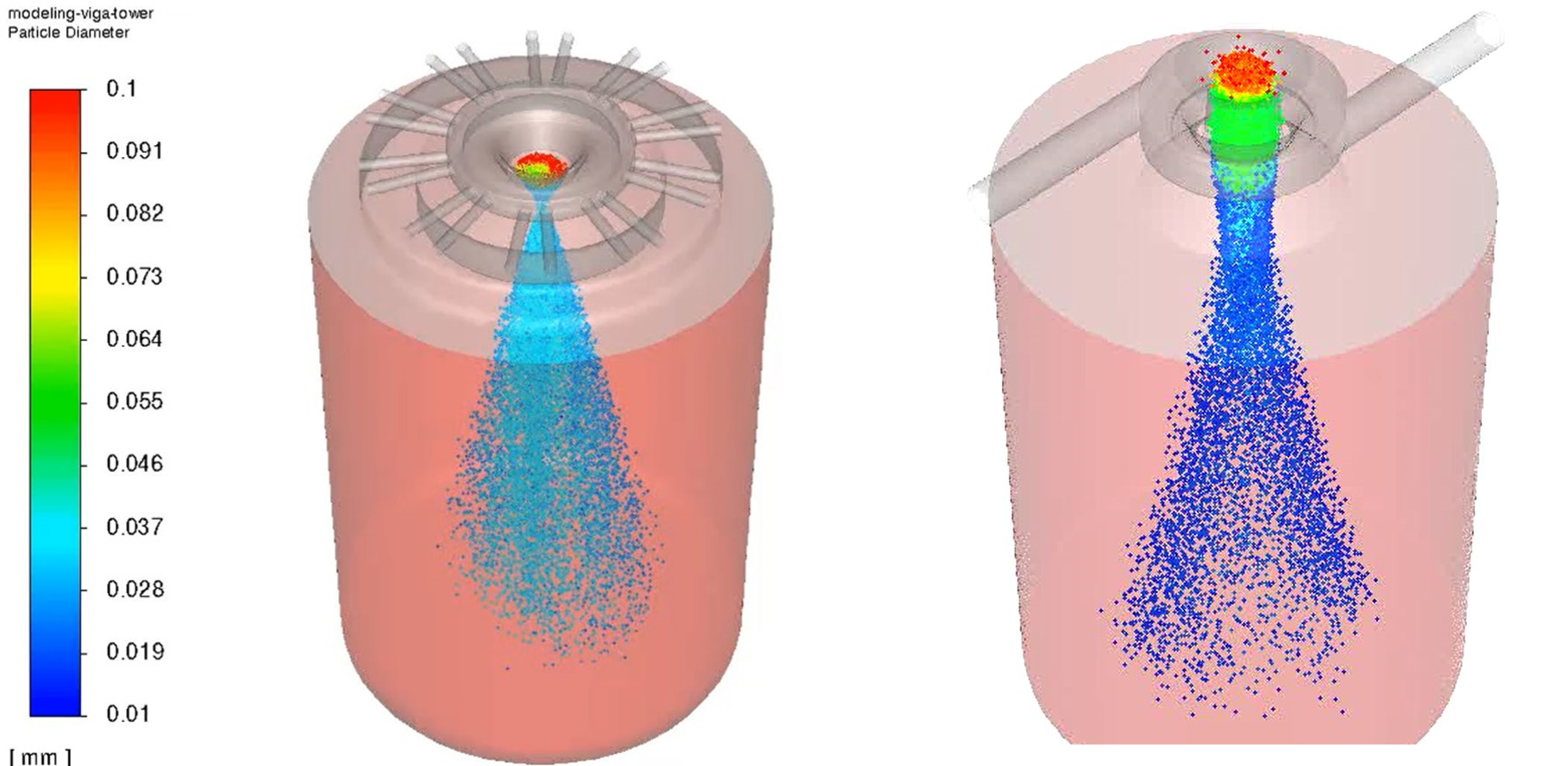
Figure 1 : Modélisation numérique de l’écoulement métallique dans la tour d’atomisation VIGA (gauche) et EIGA (droite).
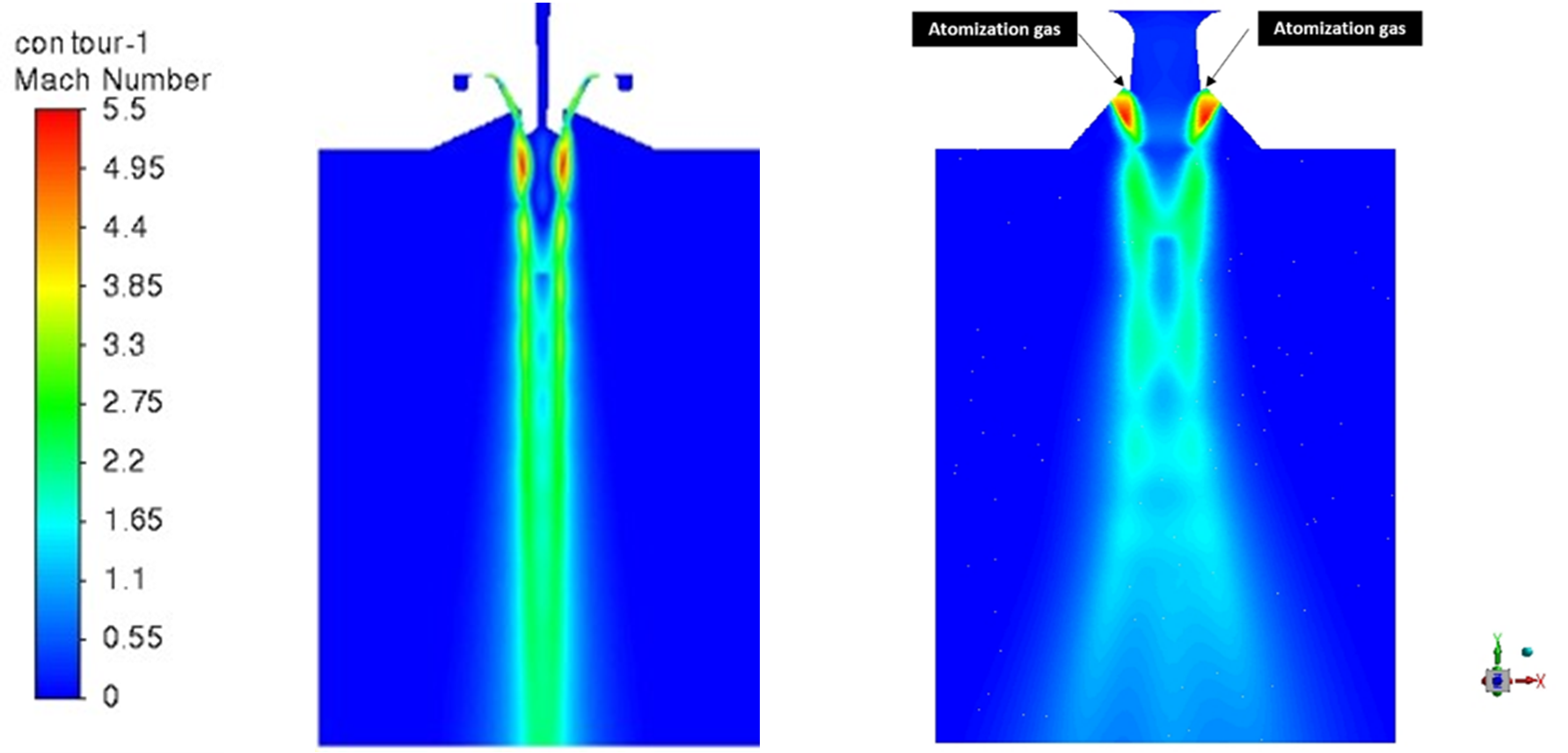
Figure 2 : Simulation numérique de l’écoulement gazeux dans la tour d’atomisation VIGA (gauche) et EIGA (droite).
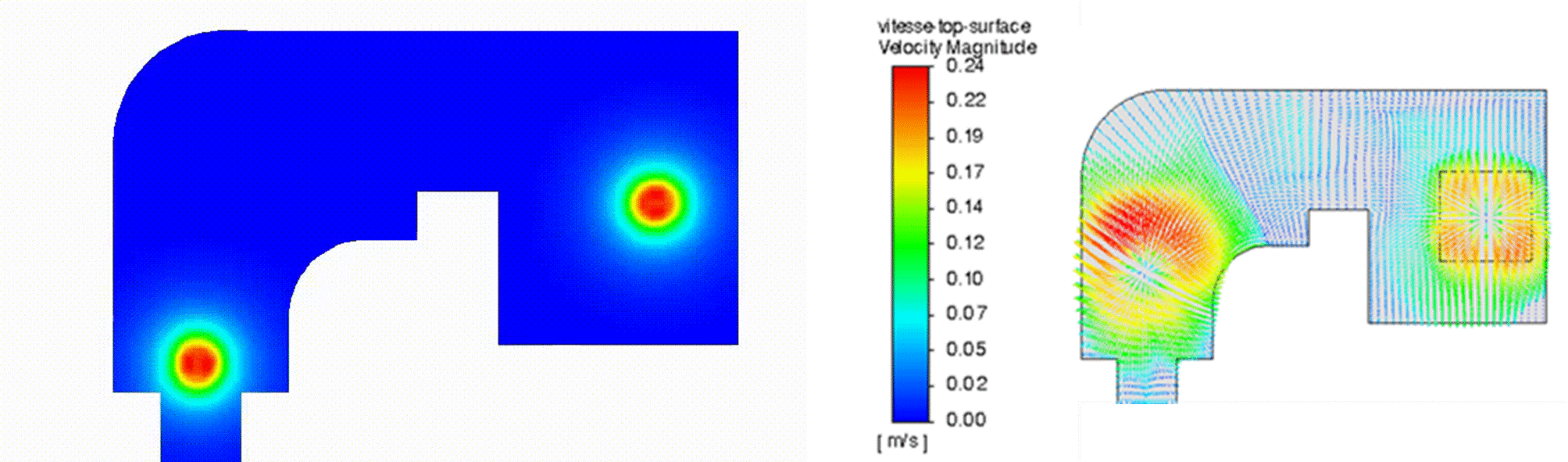
Figure 3 : Simulation numérique du four PAMCHR
Simulation des procédés d’assemblage multi-matériaux
L’activité « Assemblage multi-matériaux » a émergé en réponse à la problématique de l’allègement des structures automobiles pour la diminution des émissions polluantes. L’utilisation d’alliages légers (comme l’aluminium) et de tôles d’acier à très haute résistance mécanique d’épaisseurs réduites impose l’adoption de nouvelles techniques d’assemblage, en remplacement du soudage par point historiquement utilisé.
Ainsi, l’IRT M2P s’est doté d’effecteurs de clouage, de fluo-vissage, de clinchage, de rivetage auto-poinçonneur creux et plein ainsi qu’une plateforme permettant l’étude du procédé de soudage d’inserts envisagés par cette industrie. Ces procédés sont extensivement étudiés expérimentalement par cette activité qui possède toutes les briques technologiques pour leur mise en œuvre à l’échelle d’éprouvette monopoint jusqu’au démonstrateur technologique.
Par ailleurs, ces procédés sont très rapides, fortement multi-physiques et confinés en termes de dimensions. La compréhension fine des couplages multi-physiques et des phénomènes locaux aux interfaces entre les éléments mécaniques et les tôles passe par des simulations numériques des procédés calées sur les mesures physiques.
Apports de la simulation numérique
La simulation numérique joue un rôle essentiel dans la compréhension et l’optimisation de ces procédés d’assemblage. Elle nous permet de :
- Prédire l’impact des paramètres d’assemblage sur la qualité des jonctions.
- Visualiser les phénomènes physiques invisibles en temps réel.
- Analyser les interactions multi-physiques complexes (thermomécaniques, électromagnétiques, etc.).
- Identifier les configurations optimales pour garantir la robustesse et la durabilité des assemblages.
Nos simulations, réalisées sous Forge NxT4.0 ou Abaqus, permettent de modéliser avec précision l’histoire thermomécanique des assemblages. Une fois validées par des essais expérimentaux, elles servent à ajuster les paramètres des procédés pour optimiser leur intégration industrielle. Toutefois, cette technique précise au niveau d’une jonction mono-point et souhaitable d’un point de vue de la compréhension physique reste inadaptée à des calculs de structure multipoints avec des géométries de pièces complexes (maillages trop fin et complexes). Ainsi, des modèles 1D sont développés sous Abaqus pour aider au dimensionnement des structures.
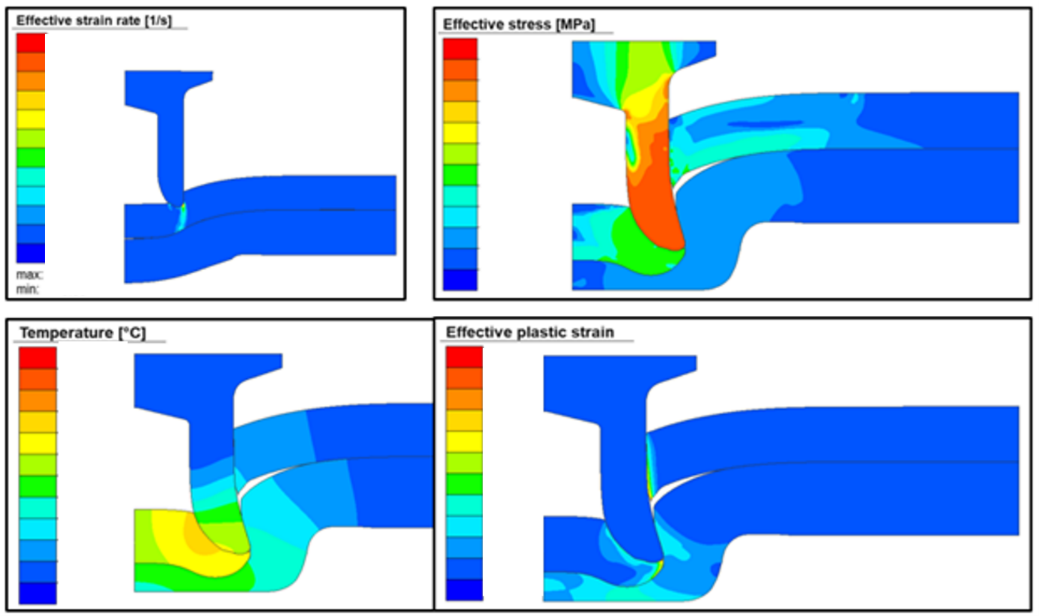
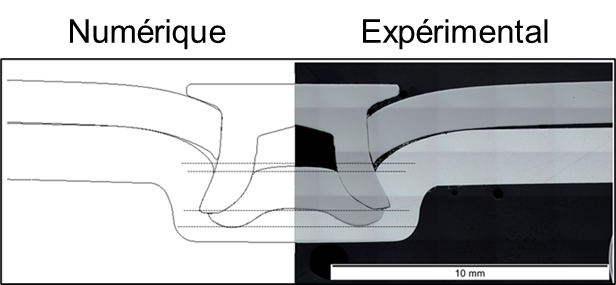
Figure 4 : Simulation numérique du procédé de rivetage
Simulation des procédés des traitements thermiques et thermochimiques
Les traitements thermiques et thermochimiques sont des procédés visant conférer aux pièces mécaniques les propriétés mécaniques souhaitées pour résister aux sollicitations subies en service. L'un des enjeux majeurs de ce domaine est de pouvoir faire le lien entre les paramètres du procédé appliqués, les microstructures obtenues et les propriétés mécaniques résultantes. La connaissance et maîtrise de cet enchaînement est donc primordiale, à plus forte raison dans un contexte où les exigences de performances associées à des contraintes de réduction de coût et de sobriété énergétique sont de plus en plus présentes.
Cependant, la mise au point de nouvelles gammes traitements ou l’optimisation des matériaux, leurs propriétés et des procédés existants est souvent longue et coûteuse en raison de la complexité des interactions thermiques, thermochimiques et métallurgiques. La simulation numérique s’impose comme un levier clé pour accélérer ces développements et maîtriser précisément les phénomènes en jeu.
Principaux procédés thermiques et thermochimiques simulés
Afin de soutenir les développements dans ce domaine, l’IRT M2P a investi dans un parc de plateformes (allant de l’échelle laboratoire à l’échelle industrielle) permettant de couvrir un large de panel de procédés :
- Les procédés de trempe
La trempe consiste à refroidir brutalement un matériau chauffé afin de modifier sa structure et d’augmenter sa dureté. Plusieurs types de trempe peuvent être simulés :
- Trempe à l’air :
- Modélisation des vitesses locales du fluide et de l’hétérogénéité du refroidissement.
- Détermination du coefficient d’échange thermique h(x,t) en fonction de la vitesse de l’air et de la géométrie de la pièce.
- Évaluation des gradients thermiques internes et de leur impact sur les distorsions et contraintes résiduelles.
- Trempe à l’eau :
- Détermination par méthode inverse des conditions aux limites sous forme de flux de chaleur extrait jq(x,t) ou de coefficients de transfert de chaleur h(x,t).
- Modélisation des champs de température dans tout le volume de la pièce, cf. Figure 5.
- Estimation de la fraction locale des phases métallurgiques (martensite, bainite, ferrito-perlite, austénite).
- Évaluation des déformations et contraintes résiduelles.
- Trempe par induction (ou par contours) :
- Intégration du couplage électromagnétique, thermique et métallurgique pour optimiser le profil de chauffe et de refroidissement, cf. Figure 6.
- Modélisation du champ électromagnétique pour ajuster la profondeur de chauffe et l’uniformité du champ thermique.
- Calcul des flux thermiques générés par effet Joule dans la pièce.
- Détermination du coefficient d’échange thermique local pendant la phase de trempe.
- Évaluation des contraintes résiduelles induites.
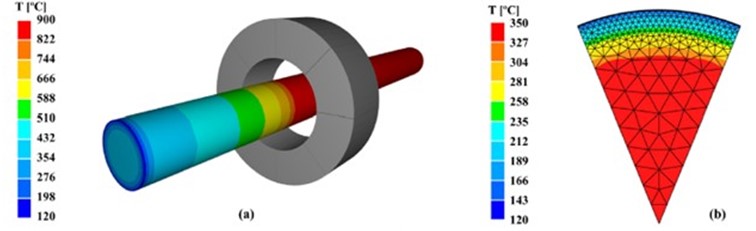
Figure 5 : Simulation éléments finis, réalisée sous Forge NxT 4.0 ® : (a) modélisation 3D d’une barre en acier refroidie par les jets de l’anneau de trempe représenté en gris, (b) tranche de barre montrant la température interne après défilement au travers de l’anneau de trempe.
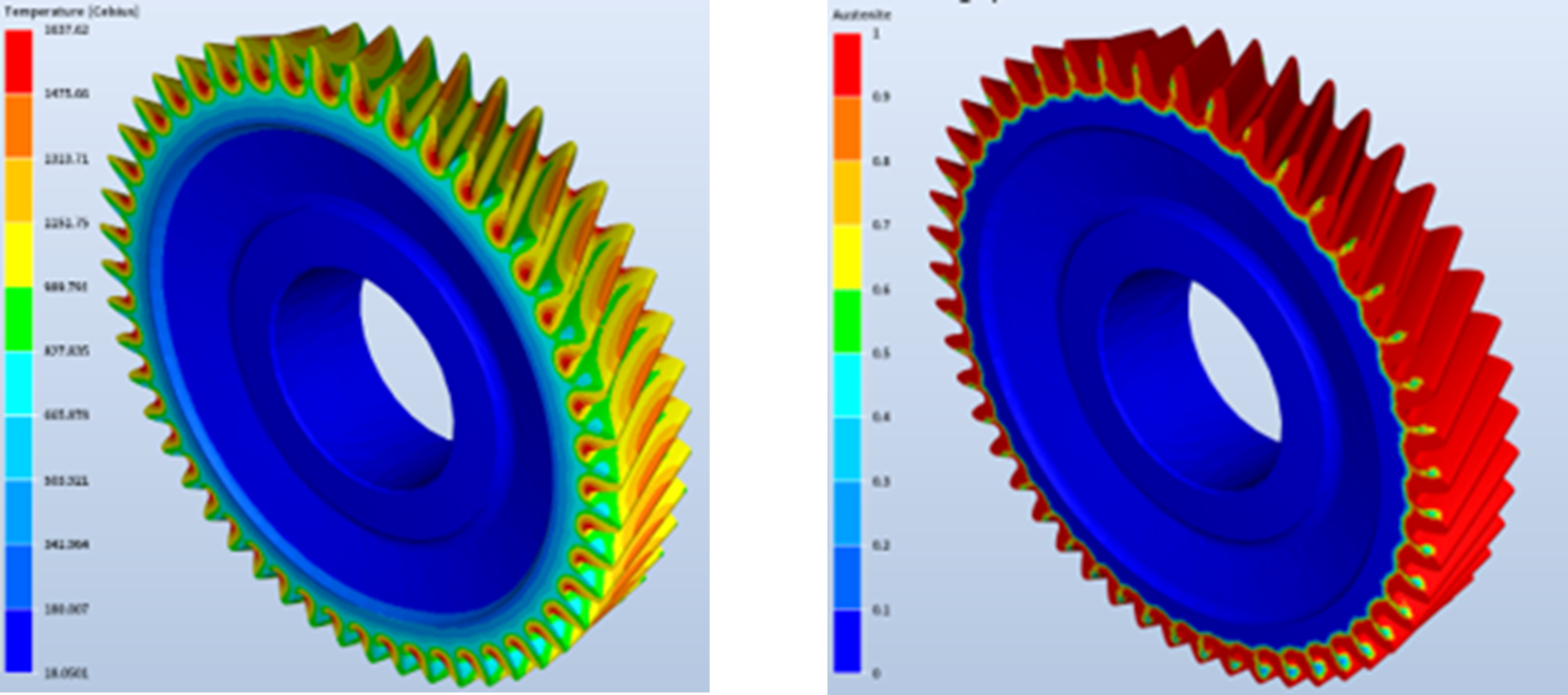
Figure 6 : Simulation éléments finis, réalisée sous Forge NxT 4.0 ® : Modélisation 3D de la chauffe par induction d'un pignon, montrant l'évolution de la température (gauche) et l'évolution métallurgique (droite).
- Les traitements thermochimiques
Ces procédés permettent l’enrichissement de la surface des pièces en éléments spécifiques (carbone, azote). Cette dénomination regroupe les notamment les procédés suivants :
- Cémentation et carbonitruration atmosphérique
- Cémentation et carbonitruration basse pression
- Nitruration gazeuse en phase ferritique ou austénitique
- Nitrocarburation gazeuse
Tous ces procédés ont en commun d’être régis par des phénomènes et mécanismes complexes activés thermiquement. De fait, il est possible de simuler ces traitements thermiques et ces enrichissements en carbone/azote de manière précise avec des outils de simulations thermodynamiques, tels que la suite logicielle ThermoCalc® et son module Dictra®, ou multi-physiques tels que la suite logicielle Forge® pour le traitement thermique. Ces simulations permettent notamment de décrire :
- Les transformations de phase et phénomènes de précipitation ayant lieu au sein de la pièce traitée au cours du cycle thermique appliqué.
- La cinétique de transfert de matière entre la phase gazeuse et la pièce traitée.
- Les profils de diffusion dans l’état solide lors des cycles d’enrichissements en carbone et/ou azote.
Impact global de la simulation numérique
L’intégration de la simulation numérique dans les activités de l’IRT M2P a transformé la manière dont les procédés métallurgiques sont conçus et optimisés. Parmi les principaux avantages, on note :
- Optimisation des paramètres : réduction du nombre d’essais physiques grâce à une validation préalable sur modèle.
- Gain de temps et réduction des couts : optimisation des cycles de production et diminution des erreurs.
- Amélioration de la qualité des matériaux : meilleure homogénéité et réduction des défauts.
- Amélioration de la qualité : prévision des performances mécaniques et identification des zones critiques avant fabrication.
- Accélération de l’innovation : développement de nouveaux alliages, optimisation des produites et prise en compte plus rapide des nouvelles technologies
- Précision accrue : meilleures performances des alliages grâce à une maîtrise optimisée des procédés.
Sans l’apport de la simulation numérique, l’optimisation des procédés serait un véritable défi. Les essais physiques seraient plus nombreux, coûteux et chronophages. La variabilité des résultats rendrait difficile la maîtrise des propriétés finales des matériaux, impactant ainsi la performance et la compétitivité industrielle.
Conclusion
L’IRT M2P met la simulation numérique au service de l’innovation et de l’optimisation des procédés métallurgiques. Grâce à une approche combinant expérimentation et modélisation avancée, nous accompagnons nos partenaires industriels dans la conception de nouvelles poudres métalliques, l’optimisation des procédés de fusion et la maîtrise des matériaux métallurgiques avancés. Plus qu’un simple outil, la simulation numérique est un levier stratégique pour repousser les limites de la métallurgie, améliorer la durabilité des matériaux et répondre aux défis industriels de demain. En intégrant ces technologies à grande échelle, l’IRT M2P accélère l’adoption industrielle des innovations, garantissant ainsi des solutions plus performantes et durables pour l’industrie de demain.
Références :
- B. Qaddah, P. Chapelle, J-P. Bellot, J. Jourdan, N. Rimbert, A. Deborde, R. Hammes, A. Franceschini, Swirling supersonic gas flow in an EIGA atomizer for metal powder production: Numerical investigation and experimental validation, Jo. of Mat. Proc.Tech., Vol. 311, 2023
Consulter l'article - B. Qaddah, P. Chapelle, B. Dussoubs, N. Rimbert, A. Piaget, A. Arbab, P. Lamesle, Numerical Simulation Of The Impact Of Gas Type On Supersonic Gas Flow In A VIGA Atomizer For Metal Powder Production, Conference: Euro Powder Metallurgy 2024 Congress & Exhibition, 2024
Consulter l'article - W. Ayadh, J-S. Kroll-Rabotin, J-P Bellot, R. Marin, J. Delfosse, A. Cardon, A. Biagi, S. Hans, A comprehensive numerical modelling of plasma arc melting (PAM) process and simulation of inclusion removal, LMPC2024, 2024.
- A.V.S. Oliveira, D. Maréchal, D. Lawrjaniec, M. Gradeck, Sweeping water jet ring quenching of a large steel bar near industrial conditions, Appl. Therm. Eng., Vol. 263, 2025, 125305
Consulter l'article