Modélisation et simulation numérique du comportement mécanique et des procédés de mise en œuvre des composites
Contexte
La simulation numérique des composites est un outil clé pour comprendre, prédire et optimiser le comportement mécanique et les procédés de mise en œuvre. Il s’agit de corréler les essais avec les calculs, de lever des verrous technologiques en proposant et en analysant des concepts innovants, et d’optimiser la conception ou d’améliorer le procédé composite. Il s’agit également de développer des modèles mathématiques prédictifs de substitution aux simulations numériques physiques avec la science des données. La simulation numérique favorise ainsi l’aide à la décision lors du choix des solutions.
L’objectif de la simulation numérique du comportement mécanique des composites est de réduire la masse des structures tout en améliorant la performance mécanique. En effet, les matériaux composites, de type polymères renforcés de fibres, sont des matériaux constitués d’au moins deux matériaux différents formant un mélange hétérogène présentant une performance améliorée. Ainsi, la masse volumique d’un composite carbone-epoxy est de 1.5 g/cm3 contre 7.8 g/cm3 pour un acier.
La simulation numérique joue également un rôle majeur dans l’amélioration des procédés d’injection liquide (RTM, C-RTM), lesquels permettent une cadence de production souvent meilleure que les autres procédés composites. Il s’agit alors d’améliorer les conditions d’injection de façon à éviter les porosités ou zones sèches dans la pièce, alors que les essais d’injection se déroulent en moule fermé ce qui rend difficile l’observation directe de l’imprégnation des fibres par la résine. La simulation numérique permet ainsi de réduire le nombre de moules à fabriquer ce qui réduit les coûts de développement et de production.
Plus généralement, la simulation numérique vise à réduire le nombre d’essais et de prototypes à fabriquer, et à réduire les temps et coûts de développement par rapport à des démarches exclusivement empiriques ou par essais-erreur. Elle a pour objectif d’améliorer la compétitivité des produits et des procédés industriels.
Exigences
Les pièces composites doivent répondre par exemple à des réglementations, des normes d’essais et également des exigences internes telles que le cahier des charges. Ces exigences portent sur la performance mécanique, la faisabilité industrielle et les délais de développement. Les simulations doivent également prendre en compte la géométrie du produit avec possibilité de la redéfinir si nécessaire, les propriétés des matériaux, souvent déterminées par essais ou issues de bases de données bibliographiques, et les temps de calcul, influençant parfois la faisabilité et l’intégration dans le processus industriel.
Contenu
Simulation du comportement mécanique
La simulation numérique du comportement mécanique peut être réalisée par exemple en statique linéaire (relation force – déplacement linéaire) et non linéaire (en cas de frottement ou de grands déplacements par exemple). La simulation des composites en dynamique non linéaire peut également être envisagée (crash, impact, choc).
Par ailleurs, plusieurs types d’optimisation des composites sont possibles et jouent un rôle essentiel dans la résolution du problème :
- Optimisation topologique : identification de la meilleure répartition de la matière dans un volume déterminé, et donc de la meilleure géométrie de la pièce compte tenu des sollicitations mécaniques.
- Optimisation des épaisseurs et orientations des fibres : identification des configurations offrant les meilleures performances mécaniques.
- Optimisation paramétrique : identification des propriétés mécaniques optimales du matériau composite par exemple.
L’intégration de la science des données accélère ces analyses et permet des calculs en temps réel en développant des modèles mathématiques prédictifs de substitution aux simulations numériques mécaniques.
Simulation des procédés de mise en œuvre
La modélisation et la simulation numérique des procédés composites porte principalement sur les procédés d’injection de résine dans un renfort fibreux poreux :
- RTM (Resin Transfer Moulding) : simulation de l’injection de la résine dans le renfort fibreux poreux de façon à comprendre les chemins de remplissage, prédire la durée du procédé, et éviter la présence de zones sèches dans la pièce en fin de procédé. Un calcul peut durer quelques heures ou quelques jours par exemple et permet de définir et d’améliorer les conditions d’injection. La perméabilité du renfort fibreux doit être préalablement prise en compte en simulation et peut être déterminée expérimentalement.
- C-RTM (Compression Resin Transfer Moulding) : prise en compte de la compression du renfort pour accélérer l’imprégnation et améliorer la qualité finale. Le moule est légèrement entrouvert et la résine est injectée dans cet espace, puis le renfort fibreux est comprimé par le moule ce qui accélère son imprégnation par la résine et la durée du procédé. Des améliorations des positions des zones d’injection et d’évents peuvent par exemple être proposées pour éviter les zones sèches.
- Il est également possible de simuler les distorsions dans la pièce induites par la cuisson de la résine de façon à respecter les exigences dimensionnelles sur la pièce composite.
Démarche générale
La démarche générale commence typiquement par une étude bibliographique permettant d’identifier l’existant. La modélisation et la simulation sont ensuite réalisées sur des démarches préliminaires permettant de lever des verrous technologiques en réalisant des preuves de concepts, de pré dimensionner des couples produit-procédé, et d’aider à la décision pour le choix de la solution à développer. Des simulations plus détaillées peuvent être réalisées par la suite sur des projets R&D plus longs. La corrélation essais/calcul permet de vérifier les simulations numériques. La simulation numérique et l’optimisation sont alors utilisées pour satisfaire les exigences et réaliser les livrables dans les délais définis.
Exemples de réalisations
Simulation du comportement mécanique
Concernant le comportement mécanique des matériaux, la simulation numérique a permis d’identifier des géométries et matériaux répondants aux exigences tout étant fabricables. Par exemple, de l’optimisation topologique d’une pièce composite a été réalisée avec la contrainte d’une section constante pour permettre la fabrication en pultrusion. Dans un autre exemple, des bilans en termes de masse, de coûts ou encore de CO2 ont été réalisés en faisant varier les matériaux constituant le composite et en optimisant les épaisseurs par orientation, indiquant des réductions significatives sur les designs optimisés. Les logiciels de calculs peuvent être couplés à un logiciel de science des données ce qui a permis de réaliser des études de sensibilités, des modèles mathématiques prédictifs de substitution, et de l’optimisation paramétrique. L’étude de sensibilité permet d’identifier et de se focaliser sur les paramètres les plus influents lors des analyses subséquentes. Les modèles mathématiques de substitution permettent de trouver des compromis sur le design composite et de capitaliser l’expérience acquise. L’optimisation paramétrique a été utilisée pour identifier des optimums sur les paramètres matériaux par exemple.
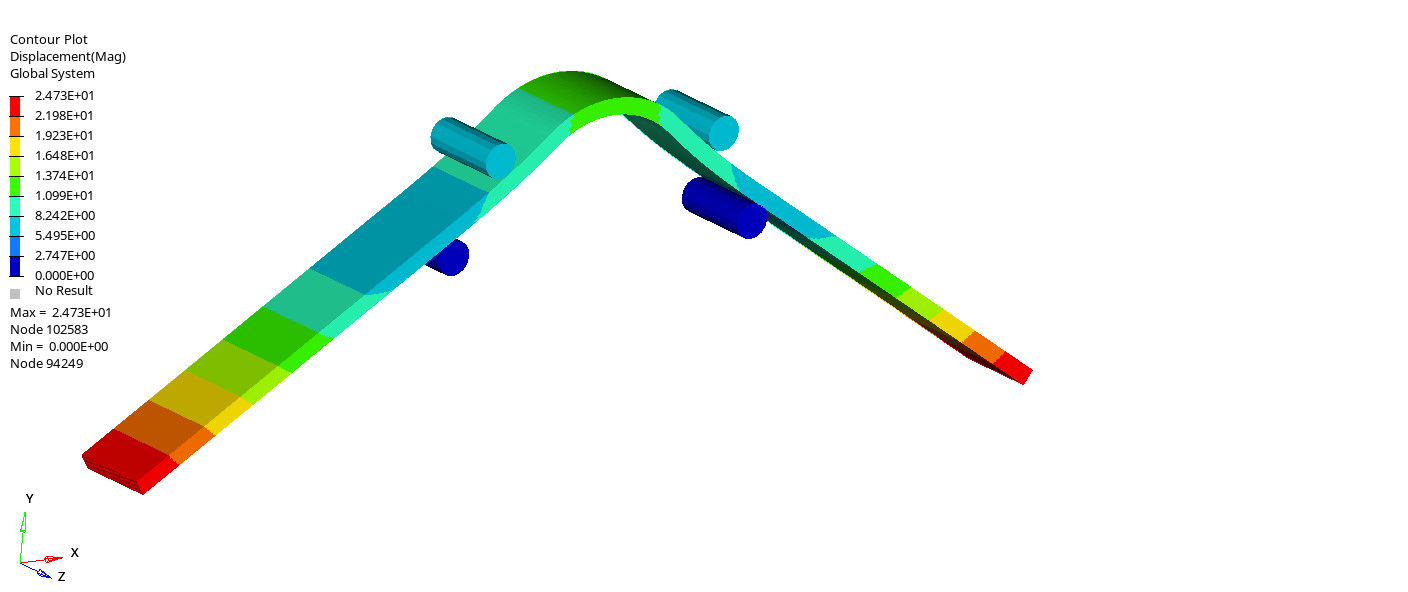
Simulation des procédés de mise en œuvre
Concernant les procédés de mise en œuvre, la modélisation a permis par exemple se limiter à quelques essais élémentaires permettant de calibrer un modèle matériau pour la simulation RTM lorsque des centaines voire des milliers d’essais auraient été potentiellement nécessaires dans une approche exclusivement expérimentale de recalage des données matériaux. Une telle quantité d’essais aurait occasionné des coûts et temps de développement inenvisageables. Dans un autre exemple, la simulation numérique RTM a permis de définir des zones d’évent nécessaires sur des moules avant leur fabrication, de façon à éviter des fermetures de front de résine dans la pièce à fabriquer. Cela a non seulement permis d’obtenir une pièce satisfaisante en fabrication, mais également de fabriquer un moule satisfaisant du premier coup.
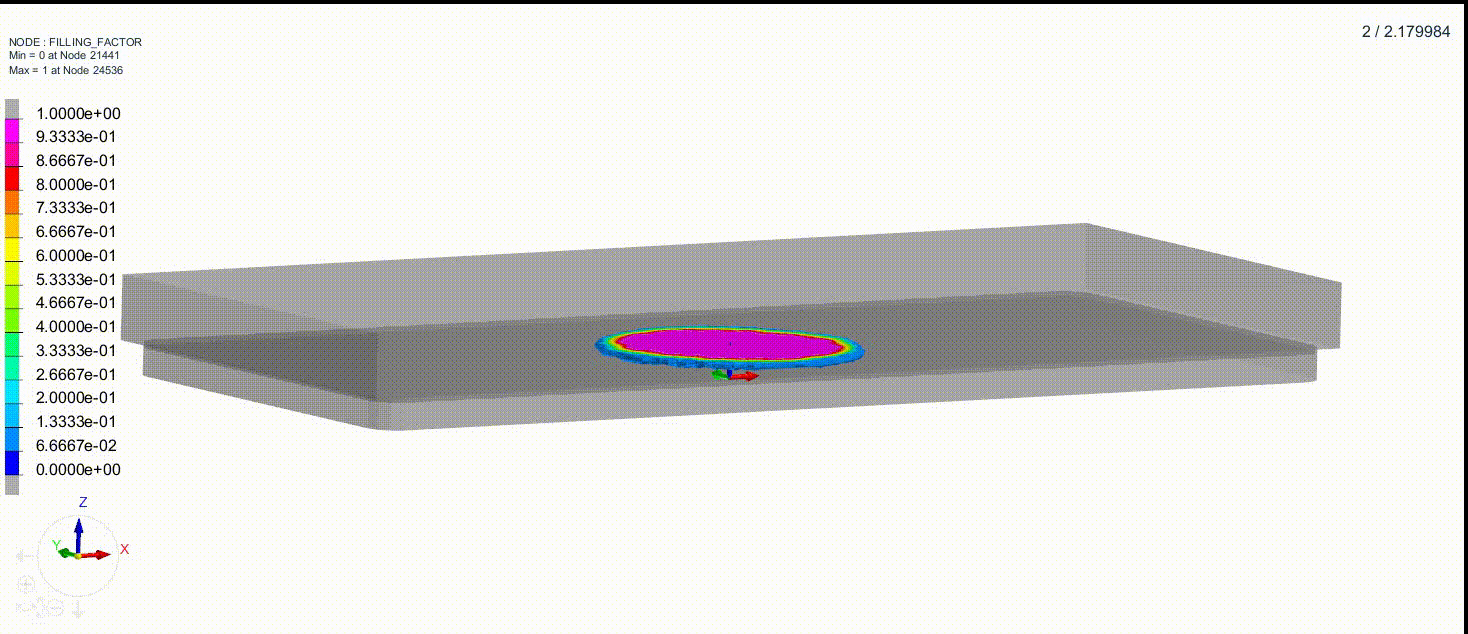