Traitements de surface : l'IRT M2P investit dans un nouvel équipement pour le procédé de parachèvement par recirculation
L’IRT M2P renforce son expertise R&D dans le domaine des traitements de surface en investissant dans un équipement unique sur son site de Duppigheim. Investi dans le cadre du projet NEMO et conçu par SIMETS, partenaire du projet et fabricant d’équipements et de lignes de traitements de surface sur mesure, notre nouveau pilote de recirculation permet le traitement des surfaces internes de pièces par recirculation avec différentes solutions chimiques.
Le polissage chimique dans AFTER ALM et NEMO
Le projet NExt alM finishing prOcesses (NEMO) consiste à la montée en maturité et à l’optimisation de procédés de parachèvement développés dans le cadre du projet AFTER ALM, achevé en décembre 2021, en vue d’un transfert technologique chez les partenaires industriels. Parmi l’ensemble des procédés de parachèvement étudiés dans NEMO, les résultats issus des nombreux essais menés sur pièces réelles ou démonstrateurs montrent une réelle efficacité du polissage chimique pour un traitement homogène des pièces complexes (présence de cavités ou de canalisations simples).
Défis rencontrés
Si le traitement par immersion simple permet de parachever l’intérieur d’une grande diversité de pièces complexes, le procédé de polissage chimique peut tout de même rencontrer certaines limites d’accessibilité pour des pièces dont les canalisations sont trop fines ou trop tortueuses pour permettre l’écoulement naturel du bain (par exemple, des échangeurs de chaleurs ou des blocs hydrauliques). De plus, l’hydrogène généré par la réaction de dissolution peut s’accumuler dans certaines zones et empêcher la circulation de la solution chimique et, par conséquent, le traitement optimal de la pièce.
Ce verrou a rapidement été levé lors du projet AFTER ALM en forçant le passage de la solution de polissage chimique à l’intérieur des canalisations à l’aide de tuyaux et de pompes connectés en entrée et en sortie des pièces. Si de tels dispositifs ont permis le traitement de nombreuses pièces au cours des projet AFTER ALM et NEMO, leur conception « artisanale » présente 3 limites majeures :
- Absence de moyens d’instrumentation : pas ou peu de contrôle sur le débit et la quantité de solution circulant à l’intérieur des pièces ainsi que sur la température de la solution en entrée et en sortie de pièce ;
- Risque chimique potentiel : les gammes de traitement comprenant plusieurs étapes (activation, polissage, blanchiment, rinçage…), les opérateurs devaient manipuler les pièces entre chaque bain pour les déplacer et éventuellement les déconnecter/reconnecter, induisant à chaque fois un risque de perte d’étanchéité du système ;
- Procédure particulièrement chronophage en raison des différentes étapes et manipulations citées précédemment.
La solution : le pilote de recirculation
Le pilote de recirculation révolutionne le procédé de parachèvement par recirculation en répondant à ces problématiques avec la garantie d’une sécurité optimale lors des manipulations et des opérations ainsi qu’un contrôle total des paramètres de traitement. Il joue un rôle essentiel dans la phase préparatoire à l'industrialisation du procédé. L'objectif premier de cet équipement est de mener des recherches et des développements sur des procédés chimiques tout en assurant une sécurité maximale pour les utilisateurs. L’équipement comporte quatre zones distinctes :
- Une zone dédiée à la préparation des solutions chimiques. 4 cuves de 120L, dont une entièrement conçue en PVDF (polyfluorure de vinylidène), permettent de mettre en place les gammes complètes de traitement. Elles ont une gestion automatique qui inclut la régulation de température, la détection du niveau de liquide, l’agitation du bain et l'ajustement du niveau des solutions chimiques.
- Une zone technique pour le transfert des produits. 4 pompes péristaltiques pilotées indépendamment via l’écran de contrôle assurent le système de recirculation gérant des flux de l’ordre de 100 à 500 l/h à travers les canaux de la pièce.
- Une zone destinée au raccordement des pièces à traiter comportant 4 voies d'injection et 4 voies de sortie indépendantes et contrôlables, toutes équipées d'un débitmètre et d'une sonde de température. Ce système permet de traiter une pièce unique selon différentes configurations (4 entrées - 4 sorties, 4 entrées - 1 sortie, 1 entrée - 4 sorties, etc.) ou de traiter 4 pièces comportant chacune 1 entrée et 1 sortie. Dans ce second cas d’usage, c’est un moyen de faire de la compréhension de manière indépendante et contrôlée en appliquant des débits différents sur chacune des pièces.
- Une armoire électrique permettant le pilotage et l'enregistrement des données.
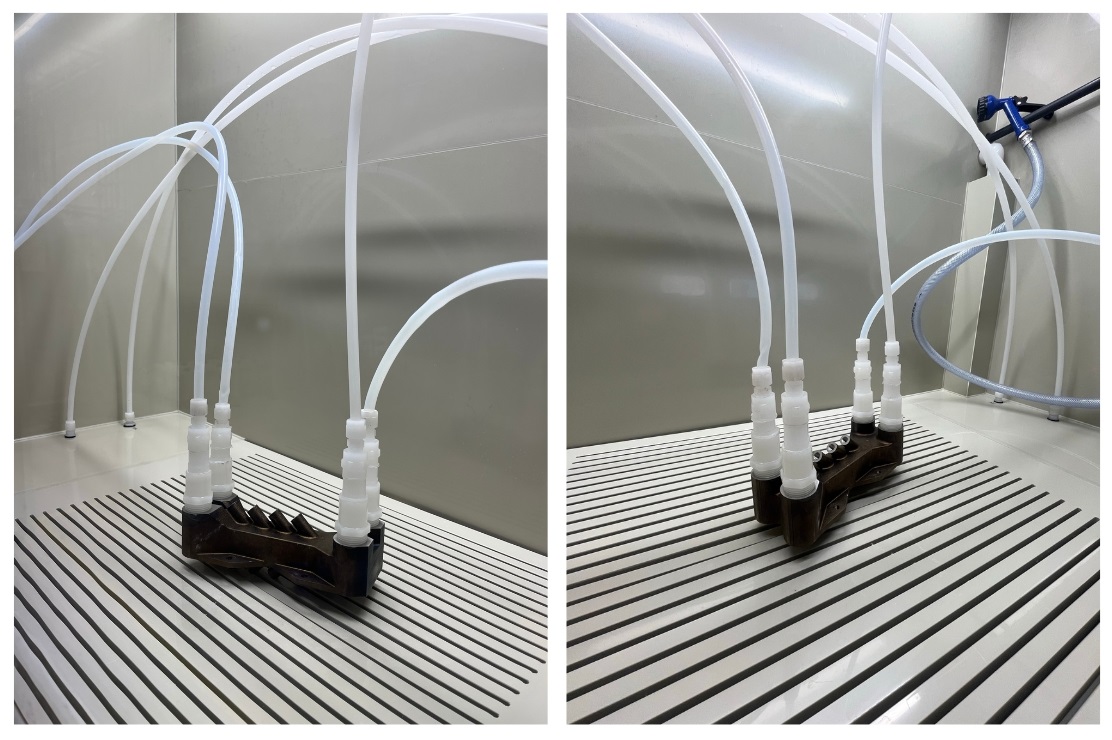
Zone de raccordement des pièces
Principales caractéristiques et avantages
- Le procédé est entièrement automatisé : toutes les étapes et paramètres de traitement sont programmés grâce un écran de contrôle. Il suffit de connecter la pièce à traiter dans la zone de raccordement avant de régler et de lancer la séquence de traitement. La pièce rincée est récupérée en fin de traitement ;
- Le système offre un contrôle et un suivi précis des paramètres de traitement (évolution du débit d’entrée et de sortie, mesures de températures d’entrée et de sortie, etc.), garantissant des données fiables et la possibilité de réaliser des campagnes d’optimisation avant transposition des résultats en externe ;
- La mise en sécurité des opérateurs grâce à la réduction des étapes manuelles et, par conséquent, des risques d’accident liés notamment aux problèmes d’étanchéité ;
- L’ensemble des cuves et de l'espace de travail est équipé d’un système d’aspiration relié à l'aspiration du réseau aéraulique du site, assurant une évacuation efficace des émanations et un environnement de travail sain pour les opérateurs ;
- En cas de fuite, le pilote dispose d’un outil de récupération permettant de renvoyer la solution vers le bain si elle est propre ou bien de l’évacuer dans un compartiment dédié.
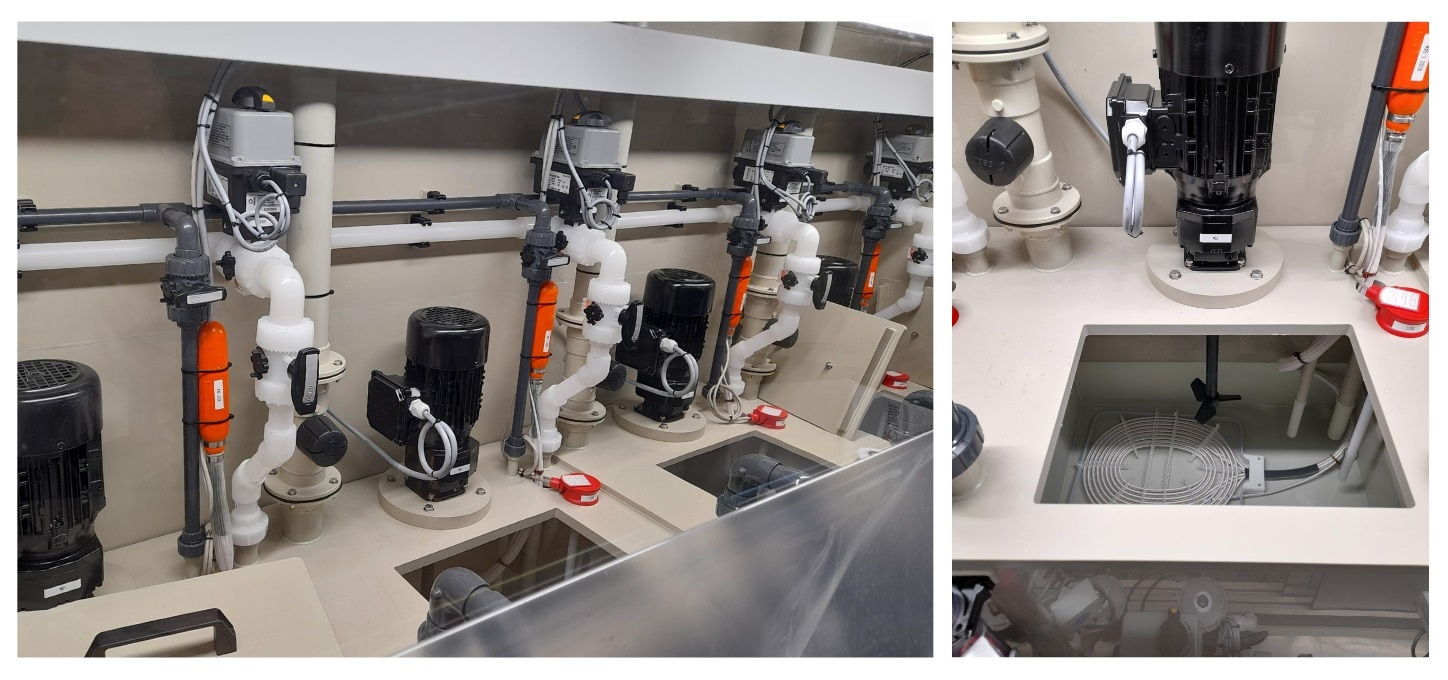
Cuves de stockage, agitateurs et trappes de visite
Applications
Le pilote peut être utilisé pour différents types d’alliages. Toutes applications nécessitant le polissage et/ou le nettoyage de surfaces internes complexes par recirculation avec différentes solutions chimiques de manière contrôlée et instrumentée peuvent être mises en œuvre, telles que :
- Le nettoyage de pièces issues de fabrication additive ou de pièces complexes utilisées pour la circulation d’huile ;
- Des prestations de polissage chimique classique ;
- Le traitement de surface, par exemple : un traitement de passivation des canalisations internes sur des aciers inoxydables ou un traitement de conversion des canalisations internes sur des aciers aluminium…
Notre pilote de recirculation représente une avancée significative dans le domaine des traitements de surface par voie humide. En combinant instrumentation, fiabilité et sécurité des opérateurs, cette nouvelle technologie offre une solution complète pour répondre aux défis de secteurs industriels variés, notamment l'aéronautique, le naval, le nucléaire, l’automobile, le médical et bien d'autres encore, requérant des parachèvements, traitements et nettoyages de surface de haute qualité.
En savoir plus sur le projet NEMO
Vous souhaitez développer un projet R&D ou mener des essais sur cette plateforme ? N’attendez plus et contactez-nous dès à présent : contact@irt-m2p.fr